A Comprehensive Guide to Nut Hot Forging Machines: Essential Insights for Manufacturers
Summary:
A Comprehensive Guide to Nut Hot Forging Machines: Essential Insights for Manufacturers
In the manufacturing industry, nut hot forging machines play a pivotal role in producing high-quality nuts that meet stringent specifications. These machines utilize advanced technology to reshape and strengthen metal, ensuring durability and precision. As the demand for robust and reliable fastening solutions
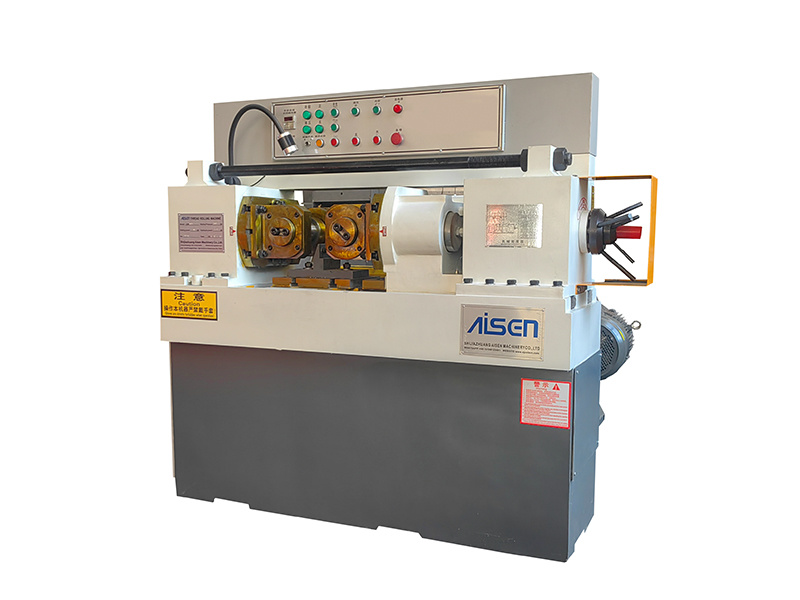
A Comprehensive Guide to Nut Hot Forging Machines: Essential Insights for Manufacturers
In the manufacturing industry, nut hot forging machines play a pivotal role in producing high-quality nuts that meet stringent specifications. These machines utilize advanced technology to reshape and strengthen metal, ensuring durability and precision. As the demand for robust and reliable fastening solutions increases, understanding the intricacies of nut hot forging machines becomes crucial for manufacturers aiming to elevate their production capabilities.
Table of Contents
- 1. Introduction to Nut Hot Forging Machines
- 2. How Nut Hot Forging Machines Work
- 3. Benefits of Using Nut Hot Forging Machines
- 4. Applications of Nut Hot Forging Machines
- 5. Key Features to Look for in Nut Hot Forging Machines
- 6. Latest Advancements in Nut Hot Forging Technology
- 7. Maintenance and Care for Nut Hot Forging Machines
- 8. Conclusion
- 9. Frequently Asked Questions
1. Introduction to Nut Hot Forging Machines
Nut hot forging machines are specialized equipment designed for manufacturing nuts from various metals, including steel, aluminum, and brass. The hot forging process involves heating the metal to a plastic state, allowing it to be shaped under high pressure. This method enhances the material's mechanical properties and ensures high precision in the final product.
Understanding the fundamentals of nut hot forging machines enables manufacturers to optimize their production processes, reduce waste, and improve overall product quality. Moreover, with the increasing complexity of fastening solutions required in various industries, investing in advanced forging technology is becoming a priority for manufacturers.
2. How Nut Hot Forging Machines Work
The functioning of nut hot forging machines can be broken down into several key stages:
Heating the Material
The first step involves heating the metal to a specific temperature, often ranging between 900 to 1200 degrees Celsius. This heating process is crucial as it makes the metal malleable, allowing it to be easily shaped.
Shaping the Metal
Once heated, the metal is placed into a die—an essential tool that defines the final shape of the nut. The machine then applies significant pressure to the material, forcing it to conform to the die's contours. This process not only shapes the nut but also aligns the grain structure of the metal, increasing its strength.
Cooling and Finishing
After shaping, the nut is cooled, often using air or water quenching, to harden the material. The final step may involve secondary processes, such as trimming, surface treatment, and quality inspection, to ensure the nuts meet specified standards.
Understanding these stages helps manufacturers improve their operational efficiency by identifying potential bottlenecks and optimizing each process.
3. Benefits of Using Nut Hot Forging Machines
The advantages of utilizing nut hot forging machines are numerous and impactful, offering manufacturers enhanced productivity and quality.
Improved Material Properties
Hot forging significantly enhances the mechanical properties of the material, resulting in stronger, more durable nuts. The process improves the material's tensile strength, fatigue resistance, and overall performance, which are critical in demanding applications.
High Precision and Consistency
Nut hot forging machines deliver exceptional precision and consistency in product dimensions. This high level of accuracy reduces the need for extensive finishing processes and minimizes waste, leading to cost savings.
Increased Production Efficiency
With automated features and rapid cycle times, these machines can produce a large volume of nuts in a short period, increasing overall production efficiency. This is particularly beneficial for manufacturers aiming to meet high demand while maintaining quality.
4. Applications of Nut Hot Forging Machines
Nut hot forging machines are widely used across various industries, showcasing their versatility and importance.
Aerospace Industry
In the aerospace sector, fasteners must meet stringent safety and reliability standards. Hot forged nuts are favored for their superior strength and resistance to stress, making them ideal for aircraft assembly.
Automotive Manufacturing
The automotive industry heavily relies on hot forged nuts for assembling components such as engines, suspensions, and body frames. The durability of these fasteners is vital in ensuring vehicle safety and performance.
Construction and Heavy Machinery
Hot forged nuts are commonly used in construction and heavy machinery applications due to their ability to withstand harsh conditions and heavy loads. Their reliability is crucial for structural integrity and operational safety.
5. Key Features to Look for in Nut Hot Forging Machines
When selecting nut hot forging machines, manufacturers should consider several key features to ensure optimal performance.
Automation Capabilities
Modern hot forging machines often come with advanced automation features, allowing for seamless operation and reduced labor costs. Automated systems can enhance consistency and reduce the potential for human error.
Energy Efficiency
Energy-efficient machines not only reduce operational costs but also help manufacturers meet sustainability goals. Look for machines that incorporate energy-saving technologies without compromising performance.
Customization Options
The ability to customize machines to suit specific production needs is essential. Features such as adjustable pressure settings, die configurations, and temperature controls can significantly impact the quality of the final product.
6. Latest Advancements in Nut Hot Forging Technology
The field of nut hot forging technology is constantly evolving, with several advancements enhancing machine capabilities and production processes.
Smart Technology Integration
The integration of smart technology enables real-time monitoring and data collection, providing manufacturers with valuable insights into their production processes. This information can be used to optimize operations and reduce downtime.
Advanced Materials
The development of new materials with improved properties allows for the production of nuts that are not only stronger but also lighter. This is particularly beneficial in industries like aerospace, where weight reduction is a critical factor.
Environmentally Friendly Practices
Sustainability is becoming increasingly important in manufacturing. Advances in hot forging technology focus on minimizing waste and reducing the carbon footprint of production processes, aligning with global efforts to promote environmentally friendly practices.
7. Maintenance and Care for Nut Hot Forging Machines
Proper maintenance of nut hot forging machines is essential for ensuring longevity and optimal performance. Here are some key maintenance practices:
Regular Inspections
Conducting routine inspections helps identify potential issues before they escalate. Regular checks on critical components, such as the heating system and dies, ensure the machine operates smoothly.
Lubrication
Consistent lubrication of moving parts reduces friction and wear, extending the life of the machine. Adhering to the manufacturer's recommendations for lubrication intervals is crucial.
Cleaning
Maintaining a clean machine environment prevents contamination and promotes efficient functioning. Regularly cleaning the machine helps avoid buildup that could affect performance.
8. Conclusion
Understanding nut hot forging machines is essential for manufacturers looking to improve their production processes and product quality. From the intricate workings of these machines to their applications across various industries, gaining insights into their functionality and benefits allows manufacturers to make informed decisions. By investing in advanced technology and adhering to proper maintenance practices, manufacturers can not only enhance efficiency but also ensure that their products meet the rigorous demands of today’s markets.
9. Frequently Asked Questions
What is the difference between hot forging and cold forging?
Hot forging involves heating the metal before shaping, which improves its ductility and allows for complex shapes with minimal defects. Cold forging, on the other hand, is performed at room temperature and is typically used for smaller, simpler parts.
What materials can be used in nut hot forging machines?
Nut hot forging machines can work with various metals, including carbon steel, stainless steel, aluminum, and brass, depending on the desired properties of the final product.
How does the heating process affect the final product?
The heating process in hot forging enhances the material's ductility, reducing the chance of cracking during shaping. It also improves the mechanical properties of the metal, resulting in a stronger finished product.
What are the advantages of using automated nut hot forging machines?
Automated machines improve production efficiency, reduce labor costs, enhance consistency, and minimize human error, allowing for higher precision in the manufacturing process.
How can manufacturers ensure the quality of forged nuts?
Manufacturers can ensure quality by implementing strict quality control measures, using advanced inspection techniques, and adhering to industry standards throughout the production process.
Latest News
AISEN Four axis nut tapping machine ready for shipment to Russia
Four axis nut tapping machine for DIN934 M8,M10 Standard hex nut is ready for shipping to Russia by land transportation.
AISEN machinery inverted wire drawing machine
We hope to cooperate with more customers for mutual development and benefits. You are welcome to contact us