Streamlining Efficiency: The Role of Welding Wire Drum Packing Machines in Manufacturing
Summary:
In the world of manufacturing, especially in sectors involving welding materials, the packing and handling of welding wire are critical for operational efficiency. A welding wire drum packing machine is designed to automate the packing process of welding wire into drums, ensuring that the product is packed securely and efficiently. This type of machinery plays a vital role in maintaining the quali
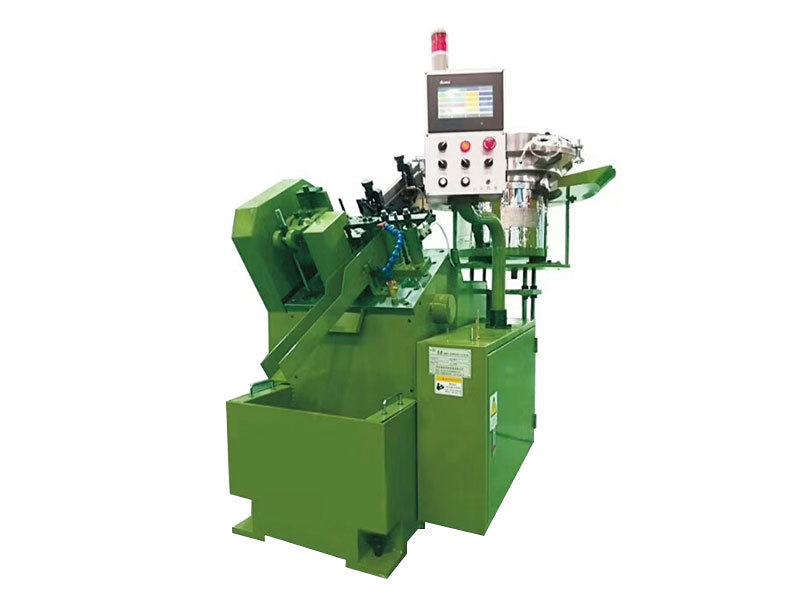
In the world of manufacturing, especially in sectors involving welding materials, the packing and handling of welding wire are critical for operational efficiency. A welding wire drum packing machine is designed to automate the packing process of welding wire into drums, ensuring that the product is packed securely and efficiently. This type of machinery plays a vital role in maintaining the quality and integrity of the welding wire while optimizing the overall packaging workflow.
One of the primary benefits of using a welding wire drum packing machine is the significant reduction in labor costs. Manual packing can be time-consuming and prone to errors, which can lead to product damage and increased rework. By automating this process, manufacturers can free up valuable human resources for other tasks, thereby enhancing productivity.
Another advantage is the consistent quality of packaging. Welding wire must be protected from moisture and contamination, which can compromise its performance. These machines are equipped with advanced technology that ensures each drum is packed uniformly, reducing the risk of damage during transportation and storage. This consistency not only protects the product but also enhances the brand's reputation for quality.
When considering the integration of welding wire drum packing machines into your manufacturing line, several factors should be taken into account. First, evaluate the production volume and choose a machine that can handle your specific throughput requirements. Additionally, consider the ease of operation and maintenance; machines that offer user-friendly interfaces and require minimal downtime for maintenance can significantly contribute to operational efficiency.
Moreover, the choice of materials used in the construction of the packing machine is crucial. Machines made from durable, high-quality materials will ensure longevity and reduce the need for frequent repairs or replacements. Furthermore, energy efficiency should be a priority; machines that consume less power can lead to lower operational costs.
It's also essential to look for features such as adjustable packing specifications, which allow for flexibility in accommodating different drum sizes or wire types. This adaptability can be invaluable for businesses looking to diversify their product offerings or respond to changing market demands.
In conclusion, a welding wire drum packing machine is an invaluable asset in the manufacturing sector, particularly for those dealing with welding materials. By automating the packing process, businesses can enhance efficiency, reduce waste, and maintain high product quality. As the industry continues to evolve, investing in advanced packaging solutions will be key to maintaining a competitive edge.
One of the primary benefits of using a welding wire drum packing machine is the significant reduction in labor costs. Manual packing can be time-consuming and prone to errors, which can lead to product damage and increased rework. By automating this process, manufacturers can free up valuable human resources for other tasks, thereby enhancing productivity.
Another advantage is the consistent quality of packaging. Welding wire must be protected from moisture and contamination, which can compromise its performance. These machines are equipped with advanced technology that ensures each drum is packed uniformly, reducing the risk of damage during transportation and storage. This consistency not only protects the product but also enhances the brand's reputation for quality.
When considering the integration of welding wire drum packing machines into your manufacturing line, several factors should be taken into account. First, evaluate the production volume and choose a machine that can handle your specific throughput requirements. Additionally, consider the ease of operation and maintenance; machines that offer user-friendly interfaces and require minimal downtime for maintenance can significantly contribute to operational efficiency.
Moreover, the choice of materials used in the construction of the packing machine is crucial. Machines made from durable, high-quality materials will ensure longevity and reduce the need for frequent repairs or replacements. Furthermore, energy efficiency should be a priority; machines that consume less power can lead to lower operational costs.
It's also essential to look for features such as adjustable packing specifications, which allow for flexibility in accommodating different drum sizes or wire types. This adaptability can be invaluable for businesses looking to diversify their product offerings or respond to changing market demands.
In conclusion, a welding wire drum packing machine is an invaluable asset in the manufacturing sector, particularly for those dealing with welding materials. By automating the packing process, businesses can enhance efficiency, reduce waste, and maintain high product quality. As the industry continues to evolve, investing in advanced packaging solutions will be key to maintaining a competitive edge.
Latest News
AISEN Four axis nut tapping machine ready for shipment to Russia
Four axis nut tapping machine for DIN934 M8,M10 Standard hex nut is ready for shipping to Russia by land transportation.
AISEN machinery inverted wire drawing machine
We hope to cooperate with more customers for mutual development and benefits. You are welcome to contact us