Innovative Techniques in U Bolt Bending: Enhancing Efficiency for Modern Manufacturing
Summary:
Innovative Techniques in U Bolt Bending: Enhancing Efficiency for Modern Manufacturing
Table of Contents
1. Introduction to U Bolt Bending Techniques
2. Importance of U Bolt Bending in Manufacturing
3. Traditional Methods of U Bolt Bending
4. Innovative Techniques Revolutionizing U Bolt Bending
4.1 Automation and CNC Technology
4.2 Advanced Materia
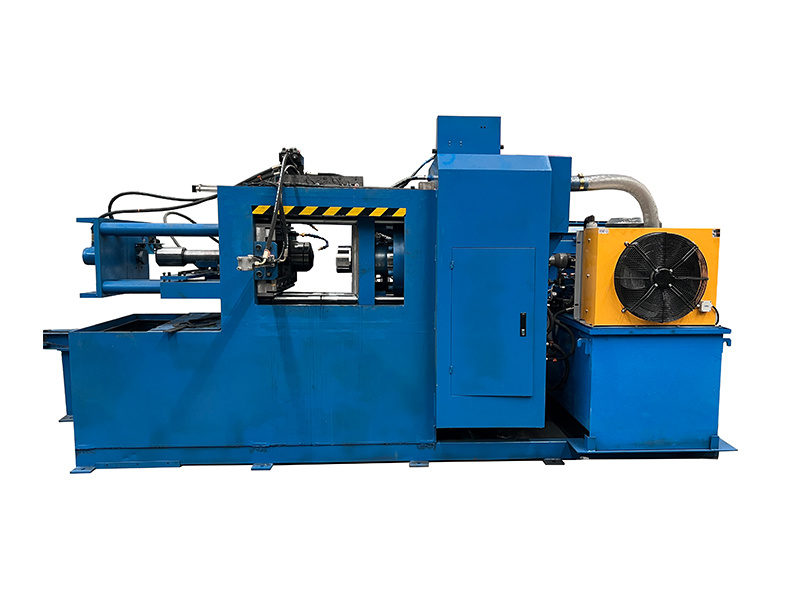
Innovative Techniques in U Bolt Bending: Enhancing Efficiency for Modern Manufacturing
Table of Contents
- 1. Introduction to U Bolt Bending Techniques
- 2. Importance of U Bolt Bending in Manufacturing
- 3. Traditional Methods of U Bolt Bending
- 4. Innovative Techniques Revolutionizing U Bolt Bending
- 4.1 Automation and CNC Technology
- 4.2 Advanced Material Selection and Processing
- 4.3 Hybrid Bending Techniques
- 5. Enhancing Efficiency through Innovation
- 6. Case Studies: Successful Implementation of Innovative Techniques
- 7. The Future of U Bolt Bending Techniques
- 8. Frequently Asked Questions
- 9. Conclusion
1. Introduction to U Bolt Bending Techniques
In the realm of **manufacturing and fabrication**, U bolts play a crucial role. These fasteners are essential for securing items together, often utilized in various sectors, from automotive to construction. As the demand for precision and efficiency grows, the techniques used in U bolt bending must evolve. This article delves into the innovative techniques that are enhancing efficiency in U bolt bending, ensuring that manufacturers stay competitive and meet the increasing demands of the market.
2. Importance of U Bolt Bending in Manufacturing
U bolts are not just simple fasteners; they are integral components in many structures and systems. Their importance can be summarized as follows:
- **Strength and Stability**: U bolts provide exceptional strength, ensuring that components remain securely fastened under varying conditions.
- **Versatility**: They can be used in a myriad of applications, making them indispensable in many manufacturing processes.
- **Cost-Effectiveness**: Efficient bending techniques can reduce material wastage and labor costs, enhancing overall profitability for manufacturers.
Understanding the significance of U bolt bending allows manufacturers to appreciate the need for upgrading their techniques to maintain a competitive edge.
3. Traditional Methods of U Bolt Bending
Historically, U bolt bending has relied on manual processes and basic machinery. Traditional methods often involve:
- **Manual Bending**: Operators use simple jigs and hand tools, which can lead to inconsistent results and higher labor costs.
- **Limited Precision**: Standard bending methods lack the precision required for modern applications, resulting in potential quality issues.
- **Time-Consuming Processes**: Traditional techniques often require lengthy setups and adjustments, reducing overall productivity.
While these methods have served the industry for decades, the need for innovation is clear in the face of modern manufacturing demands.
4. Innovative Techniques Revolutionizing U Bolt Bending
Innovation is key to improving U bolt bending processes. Several groundbreaking techniques are currently transforming the industry.
4.1 Automation and CNC Technology
The introduction of **Computer Numerical Control (CNC)** technology has revolutionized U bolt bending. Key benefits include:
- **Increased Precision**: CNC machines offer unparalleled accuracy, ensuring that each U bolt meets strict specifications.
- **Higher Production Rates**: Automated systems can operate continuously, significantly boosting output without compromising quality.
- **Reduced Labor Costs**: Automation minimizes the need for manual labor, leading to cost savings and reduced human error.
Manufacturers investing in CNC technology are finding it indispensable for staying competitive.
4.2 Advanced Material Selection and Processing
Choosing the right materials is crucial for effective U bolt bending. Innovations in material science have led to:
- **Lightweight Alloys**: Using advanced alloys can reduce weight while maintaining strength, enhancing overall product performance.
- **Surface Treatments**: Techniques like galvanization and powder coating improve durability and corrosion resistance, extending the lifespan of U bolts.
- **Recyclable Materials**: The trend toward sustainability is pushing manufacturers to select materials that are not only effective but also environmentally friendly.
By leveraging advanced materials, manufacturers can enhance the functionality and appeal of their U bolts.
4.3 Hybrid Bending Techniques
Hybrid techniques combine traditional methods with modern technology to achieve superior results. These methods include:
- **Incremental Bending**: This technique allows for complex shapes to be formed gradually, facilitating the creation of intricate designs that traditional methods cannot achieve.
- **Multi-Axis Bending**: By allowing bends in multiple directions, manufacturers can produce U bolts with complex geometries, enhancing their functionality and application range.
- **Integrated Inspection Systems**: Incorporating real-time inspection during the bending process ensures that each U bolt meets quality standards, reducing waste and rework.
Hybrid techniques represent a significant leap forward in optimizing the U bolt bending process.
5. Enhancing Efficiency through Innovation
Implementing innovative techniques in U bolt bending can lead to substantial efficiency gains:
- **Streamlined Operations**: Automation and advanced materials reduce the time required for bending, enabling quicker turnaround times.
- **Improved Quality Control**: Enhanced precision and real-time inspections result in higher quality products, reducing defects and returns.
- **Lower Costs**: By maximizing material usage and minimizing labor, manufacturers can significantly reduce production costs.
These efficiency enhancements not only boost profitability but also position manufacturers as leaders in the industry.
6. Case Studies: Successful Implementation of Innovative Techniques
Numerous companies have successfully adopted innovative techniques in U bolt bending, demonstrating the tangible benefits of modernization.
- **Case Study 1: XYZ Manufacturing**: By integrating CNC technology into their U bolt bending process, XYZ Manufacturing increased production rates by 50% while reducing material waste by 30%. This shift allowed them to meet increased demand without sacrificing quality.
- **Case Study 2: ABC Fasteners**: ABC Fasteners implemented hybrid bending techniques, resulting in the ability to produce custom U bolts with complex geometries. This adaptability led to a 40% increase in customer satisfaction and retention.
These examples illustrate the transformative power of adopting innovative techniques in U bolt bending.
7. The Future of U Bolt Bending Techniques
As technology continues to evolve, the future of U bolt bending looks promising. Key trends to watch include:
- **Smart Manufacturing**: The integration of IoT (Internet of Things) technology will allow for smarter manufacturing processes, with machines communicating to optimize production.
- **AI and Machine Learning**: These technologies will enable predictive maintenance and further enhance precision in bending processes.
- **Sustainability**: As environmental concerns grow, the focus on developing sustainable materials and processes will become increasingly significant.
Manufacturers who embrace these trends will likely lead the industry in efficiency and innovation.
8. Frequently Asked Questions
What are U bolts used for?
U bolts are primarily used to secure items together, providing strength and stability in various applications, including automotive and construction.
How has automation improved U bolt bending?
Automation, particularly through CNC technology, has increased precision, reduced labor costs, and significantly boosted production rates in U bolt bending.
What materials are best for U bolts?
Advanced alloys that are lightweight yet strong are ideal for U bolts, along with surface treatments that enhance durability and corrosion resistance.
What are hybrid bending techniques?
Hybrid bending techniques combine traditional methods with modern technology, allowing for complex shapes and integrated quality control during the bending process.
How can manufacturers enhance efficiency in U bolt bending?
Implementing automation, selecting advanced materials, and adopting hybrid techniques can significantly enhance efficiency and reduce production costs.
9. Conclusion
Innovative techniques in U bolt bending are reshaping the manufacturing landscape. By embracing automation, advanced material selection, and hybrid techniques, manufacturers can enhance efficiency, improve quality, and reduce costs. The future of U bolt bending holds promise, with smart manufacturing and sustainability at the forefront. As the industry evolves, those who adapt and innovate will thrive, ensuring that U bolts continue to play a vital role in various applications.
Latest News
AISEN Four axis nut tapping machine ready for shipment to Russia
Four axis nut tapping machine for DIN934 M8,M10 Standard hex nut is ready for shipping to Russia by land transportation.
AISEN machinery inverted wire drawing machine
We hope to cooperate with more customers for mutual development and benefits. You are welcome to contact us